高纯氮气发生器作为半导体、医药、食品包装等领域的关键设备,其核心部件(如气动阀、过滤器)的可靠性直接影响氮气纯度、系统稳定性及使用寿命。随着工业对气体纯度与连续供应要求的不断提高,提升核心部件的可靠性成为技术研发的重点方向。
一、核心部件的故障痛点与挑战
1.气动阀:作为气体流路切换的关键执行元件,长期高频动作(部分设备日均启闭超千次)易导致密封件磨损、阀芯卡滞,引发气体泄漏或流量波动,直接降低氮气纯度;
2.过滤器:需拦截压缩空气中的油雾、颗粒物及水分,若滤芯材质抗污染能力不足或结构设计不合理,易发生堵塞或穿透,导致下游吸附塔污染,缩短分子筛寿命。
实际运行中,约60%的设备故障源于上述部件失效,亟需从材料、结构及控制技术层面突破。
二、可靠性提升的关键技术路径
针对核心痛点,需通过多维度协同优化实现性能跃升:
1.高耐磨气动阀设计:
采用陶瓷-金属复合密封材料,替代传统橡胶密封件,耐磨损寿命提升5倍以上;
引入冗余弹簧复位机构与智能行程补偿算法,降低高频动作下的阀芯偏移误差,确保启闭精度达±0.01mm。
2.抗污染过滤器升级:
开发多层复合滤芯(如PP棉+活性炭+PTFE覆膜),分级拦截不同粒径污染物,纳污量提升80%;
优化流道结构设计,采用涡流分散技术降低气流冲击压力,减少滤芯局部破损风险。
3.智能运维系统集成:
在气动阀与过滤器中嵌入压差传感器与流量监测模块,实时反馈部件状态,通过AI算法预测剩余寿命,触发预防性维护提醒。
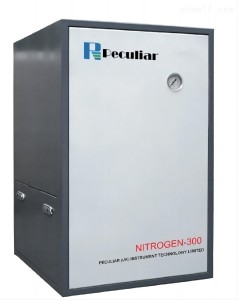
气动阀与过滤器的可靠性提升是高纯氮气发生器技术迭代的核心环节。未来,随着新材料(如自修复密封材料)、智能传感技术及数字孪生运维系统的深度融合,核心部件将进一步向没有问题的目标迈进,为高纯气体应用场景提供更稳定、高效的保障。